In today’s competitive landscape, understanding Six Sigma metrics and formulas is more than just a catchphrase—it’s a critical determinant of success for businesses aiming for operational excellence and quality improvement.
This comprehensive guide illuminates the path for professionals and enthusiasts alike seeking to demystify the complex world of Six Sigma. With its unique blend of defect opportunities, primary and secondary metrics, and an unwavering focus on reducing poor quality, Six Sigma represents a methodological approach to perfection.
Read more about Understanding Six Sigma Metrics and Formulas
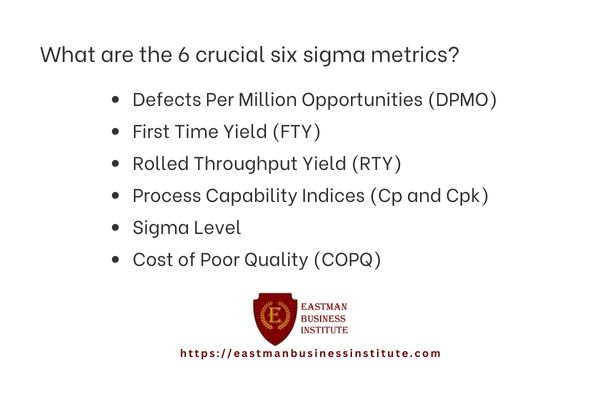
Through this article, we delve into the heart of the Six Sigma process, examining how central tendency and frequency analysis contribute to understanding the entire process of a Six Sigma project. By committing to only one primary metric for each Six Sigma method, organizations can harness the power of focused improvement, ensuring every aspect of their operation aligns with the highest standards of quality.
Join us as we explore the essential metrics and formulas at the core of Six Sigma, laying the foundation for a future where excellence is not just an aspiration but a reality.
More Things To Know About Understanding Six Sigma Metrics and Formulas
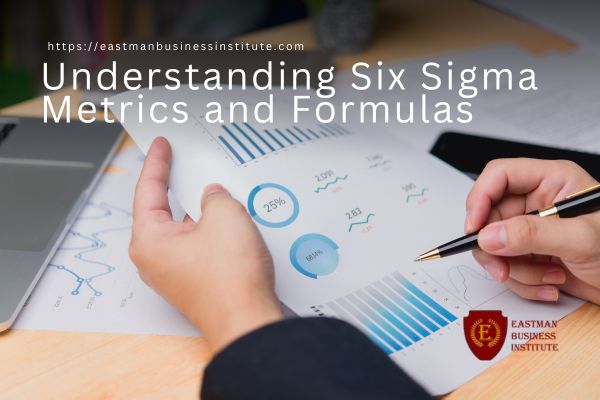
Defining Six Sigma
To define Six Sigma, you must understand its origin and purpose. Six Sigma, initially developed by Motorola in the 1980s, aims to improve processes by reducing defects to a level of 3.4 per million opportunities.
The primary goal of Six Sigma projects is to enhance quality, increase efficiency, and ultimately drive customer satisfaction. By utilizing specific methodologies and tools, such as DMAIC (Define, Measure, Analyze, Improve, Control), organizations can identify areas for improvement, set measurable goals using Six Sigma metrics, and implement data-driven solutions.
Through Six Sigma projects, businesses can streamline operations, minimize variation, and deliver consistent results, leading to sustained success and a competitive advantage in the market.
Principles of Six Sigma
By understanding the principles of Six Sigma, you can grasp the core foundation of this quality improvement methodology. Six Sigma focuses on reducing defects by improving processes and increasing efficiency. It measures process capability using sigma levels, which indicate the standard deviation from the mean performance of a process.
The sigma level corresponds to the number of defects per million opportunities. For instance, a process operating at Six Sigma has only 3.4 defects per million opportunities. Rolled Throughput Yield (RTY) is used to calculate the overall yield of a process that has multiple stages.
Understanding these key principles of Six Sigma enables organizations to systematically identify and eliminate defects, ultimately leading to higher quality and customer satisfaction.
Definition and Importance of Six Sigma Metrics
Understanding Six Sigma metrics is essential for improving processes and achieving organizational goals. In the realm of Six Sigma, metrics are used to measure process performance, defect rates, and customer satisfaction.
These metrics provide quantifiable data that organizations can analyze to identify areas for improvement and optimize their operations. By tracking metrics such as defect rates, organizations can pinpoint where processes are falling short and take corrective actions to enhance quality and efficiency.
Customer satisfaction metrics offer insights into how well products or services meet customer expectations, allowing companies to make adjustments to better meet customer needs.
Types of Six Sigma Metrics
To further enhance process improvement and achieve organizational goals, you should focus on identifying and utilizing various types of Six Sigma metrics. In the realm of Six Sigma, metrics play a crucial role in measuring process performance and identifying areas for enhancement.
Two fundamental types of Six Sigma metrics include defects per unit (DPU) and process capability. Defects per unit (DPU) quantifies the average number of defects in a product or process, providing insights into quality levels. Process capability measures the ability of a process to consistently produce output within specified limits, indicating the process’s effectiveness and potential for improvement.
Defects Per Million Opportunities (DPMO)
Calculate the Defects Per Million Opportunities (DPMO) by dividing the total number of defects by the total number of opportunities and multiplying the result by one million. When assessing DPMO, it’s crucial to understand its significance in measuring process performance.
Here are some key points to grasp the concept effectively:
- Definition: DPMO quantifies the number of defects per one million opportunities in a process.
- Primary Metrics: DPMO is one of the primary metrics used in Six Sigma methodology to evaluate process quality.
- Calculation: DPMO = (Total Defects / Total Opportunities) * 1,000,000.
- Benchmarking: Lower DPMO values indicate better process performance, with Six Sigma aiming for 3.4 defects per million opportunities.
Process Capability Index (Cp & Cpk)
Analyzing process capability through the calculation of Cp and Cpk values provides insights into the performance and potential of a system.
The process capability index, Cp, measures how well the process variation fits within the specified limits, indicating the potential for defects. A Cp value greater than 1 signifies that the process spread is smaller than the tolerance range.
Cpk considers both the process centering and spread, providing a more comprehensive view of process performance. A Cpk value greater than 1 indicates that the process mean is well-centered within the tolerance limits.
Understanding Cp and Cpk values helps organizations assess and improve their processes to meet customer requirements effectively.
First Time Yield (FTY) and Rolled Throughput Yield (RTY)
Achieve a clear understanding of First Time Yield (FTY) and Rolled Throughput Yield (RTY) by evaluating their impact on process efficiency and overall quality.
FTY measures the percentage of units that pass through a process step without any rework or defects. It helps identify areas for improvement within a single process step.
RTY calculates the overall probability of producing a defect-free unit through multiple process steps.
By analyzing standard deviation and using control charts, you can monitor the variation in FTY and RTY over time.
Improving FTY at each step enhances the overall throughput yield, ensuring higher quality outputs and increased efficiency in your processes.
Sigma Level
To determine the Sigma Level of a process, you need to assess the capability of meeting customer specifications while considering variations in quality. Sigma Level in Six Sigma metrics refers to the standard deviation of a process, indicating how well it performs within customer requirements.
The Sigma Level is calculated using formulas that consider defects per million opportunities (DPMO) or the process capability index (Cp). A higher Sigma Level signifies better process performance and fewer defects, aligning with the Six Sigma methodology’s pursuit of near-perfect quality.
Understanding Sigma Level through proper metrics and formulas allows organizations to quantify their process quality, identify areas for improvement, and strive for continuous enhancement in meeting customer expectations.
Six Sigma Formulas
Let’s discover the essential Six Sigma Formulas that are key to improving processes and achieving efficiency.
These formulas are the backbone of the Six Sigma methodology, helping you quantify performance and identify areas for improvement.
Understanding Six Sigma Formulas
When diving into the realm of Six Sigma, start by familiarizing yourself with the essential formulas. Six Sigma formulas are crucial tools in process improvement initiatives. These formulas help quantify the performance of a process and identify areas for enhancement.
Key metrics like DPMO (Defects Per Million Opportunities), Sigma level, and Yield are calculated using specific Six Sigma formulas. Understanding these formulas is fundamental to effectively measure the success of Six Sigma projects and track improvements over time.
Key Six Sigma Formulas
Transitioning from understanding the fundamental Six Sigma formulas, delve deeper into the realm of process improvement by mastering key Six Sigma formulas essential for measuring and enhancing process performance. These key formulas play a crucial role in evaluating process capabilities and identifying areas for improvement within a Six Sigma framework.
By utilizing these metrics and formulas effectively, you can quantify the current state of processes, track progress toward goals, and make data-driven decisions to optimize efficiency. Understanding the intricacies of these formulas empowers you to identify deviations, reduce defects, and enhance overall quality within your organization.
Embrace these fundamental Six Sigma formulas to drive continuous improvement and achieve higher levels of process excellence.
Formula for DPMO
To calculate the Defects Per Million Opportunities (DPMO) metric in Six Sigma, you’ll need to follow a specific formula. DPMO is a crucial measure in Six Sigma that quantifies the number of defects in a process per one million opportunities.
The formula for DPMO involves multiplying the number of defects by one million and then dividing by the total number of opportunities for defects. This formula is represented as DPMO = (Number of Defects / Total Opportunities) * 1,000,000.
Formula for Cp & Cpk
To calculate Cp & Cpk in Lean Six Sigma, you assess process capability using specific formulas.
Cp measures the process capability for a stable process with a normal distribution, comparing the spread of the process to the specification limits. The formula for Cp is (USL – LSL) / (6 * standard deviation). A Cp value greater than 1 indicates that the process spread is less than the specification limits, showing a capable process.
Cpk considers how well the processing center aligns with the specification limits. The formula for Cpk is the minimum of (USL – μ) / (3 * standard deviation) or (μ – LSL) / (3 * standard deviation), where μ is the process mean. A Cpk value greater than 1 signifies a capable process with the center aligned within the specification limits.
Formula for FTY & RTY
Calculate FTY and RTY metrics to evaluate process performance in Lean Six Sigma.
FTY, or First Time Yield, measures the percentage of processes that produce a good unit without any defects. The formula for FTY is the number of good units produced divided by the total number of units started in a process.
RTY, or Rolled Throughput Yield, evaluates the overall quality control of a process by considering the cumulative effect of multiple processes producing defective units. The RTY formula is calculated by multiplying the FTY of each individual process together.
These metrics are crucial in understanding the efficiency and effectiveness of processes within your Lean Six Sigma initiatives.
Formula for Sigma Level
The Sigma Level formula quantifies the capability of a process to perform within specified limits, building upon the foundational metrics of FTY and RTY in Lean Six Sigma.
To calculate the Sigma Level of the process output, you need to first determine the number of defects per million opportunities (DPMO). This involves counting the defects in a sample and extrapolating to a million units.
The formula for Sigma Level is then derived using the DPMO value. A higher Sigma Level indicates better process performance, with higher Sigma Levels corresponding to fewer defects and higher quality.
Understanding this formula is crucial for a Six Sigma Green Belt as it enables them to assess and improve processes to produce more defect-free units, ultimately enhancing overall efficiency and customer satisfaction.
Application of Six Sigma Metrics and Formulas
Explore practical examples where Six Sigma metrics and formulas have been applied successfully.
Discover how these tools can drive process improvement and enhance overall business performance.
Practical Examples of Six Sigma Metrics and Formulas in Use
Utilizing Six Sigma metrics and formulas can significantly enhance process efficiency and effectiveness in various industries. By applying these tools to improvement projects, organizations strive to achieve defect-free outcomes.
One practical example involves using the DMAIC (Define, Measure, Analyze, Improve, Control) methodology to reduce defects in a manufacturing process. Through the calculation of key performance indicators (KPIs) such as Defects Per Million Opportunities (DPMO) and Sigma Level, teams can pinpoint areas for improvement and track progress over time.
Formulas like Process Sigma, Yield, and Rolled Throughput Yield (RTY) provide quantifiable measures of process quality and performance. These metrics offer actionable insights that drive continuous improvement and help organizations deliver products and services that meet customer expectations.
Challenges and Solutions in Applying Six Sigma Metrics and Formulas
When applying Six Sigma metrics and formulas, you may encounter common challenges that hinder your progress. However, by implementing solutions and best practices tailored to these obstacles, you can overcome them effectively.
Stay focused on addressing these challenges to ensure the successful application of Six Sigma principles in your projects.
Common Challenges in Applying Six Sigma Metrics and Formulas
To effectively address common challenges in applying Six Sigma metrics and formulas, you need to consistently analyze and refine your processes. One challenge often faced is ensuring that the calculated process potential accurately reflects the organization’s capabilities. It’s essential to use the right formulas and metrics to determine this potential accurately.
Another common issue is correctly measuring and interpreting average defects. To tackle this, focus on selecting appropriate metrics that align with your organization’s goals and standards. Understanding the intricacies of these formulas and metrics is crucial for their successful application.
Regular training and ongoing support can aid in overcoming these challenges. By staying vigilant and continuously improving your processes, you can navigate these obstacles effectively.
Solutions and Best Practices for Overcoming Challenges
By continuously refining your processes and understanding the intricacies of Six Sigma metrics and formulas, you can effectively address challenges and implement best practices for optimal results.
When facing challenges in applying Six Sigma metrics and formulas, consider establishing clear communication channels to ensure alignment across teams.
Utilize data-driven decision-making to overcome obstacles and drive improvements.
Implement regular training sessions to enhance the understanding of Six Sigma concepts and foster a culture of continuous improvement.
Embrace a proactive approach by identifying potential issues early on and taking corrective actions promptly.
The Future of Six Sigma Metrics and Formulas
Technology is playing a pivotal role in transforming how metrics and formulas are applied and analyzed.
Stay informed and adaptable to embrace the advancements that will impact Six Sigma methodologies.
Trends Influencing Six Sigma Metrics and Formulas
Changes in technology are set to revolutionize Six Sigma metrics and formulas. As advancements in data analytics and artificial intelligence continue to evolve, the way organizations measure and analyze their performance through Six Sigma metrics is expected to become more sophisticated and real-time.
This will enable a more proactive approach to continuous improvement within organizational processes. Automation and machine learning algorithms will play a crucial role in identifying trends, predicting outcomes, and optimizing Six Sigma formulas for enhanced efficiency and effectiveness.
The Role of Technology in Six Sigma Metrics and Formulas
Technology plays a vital role in shaping the future of Six Sigma metrics and formulas. Advancements in technology have the potential to revolutionize how data is collected, analyzed, and utilized in Six Sigma projects.
By leveraging cutting-edge tools and software, organizations can streamline the process of measuring key performance indicators, identifying areas for improvement, and implementing data-driven solutions. Technology enables real-time monitoring of Six Sigma metrics, allowing for quick adjustments and continuous enhancements to formulas.
Automated algorithms and machine learning algorithms can help in identifying patterns and trends within data sets, leading to more accurate predictions and better decision-making. Embracing technology in Six Sigma not only enhances efficiency but also paves the way for continuous innovation and improvements in processes and outcomes.
Frequently Asked Questions
How Can Six Sigma Metrics and Formulas Be Applied in Non-Manufacturing Industries?
In non-manufacturing industries, you can apply Six Sigma metrics and formulas to streamline processes, reduce errors, and improve overall efficiency. Identifying key performance indicators and analyzing data will help you make informed decisions.
What Are Some Common Challenges Faced When Implementing Six Sigma Metrics and Formulas in an Organization?
When implementing Six Sigma metrics and formulas in your organization, common challenges may include resistance to change, lack of leadership support, inadequate training, and difficulty in sustaining improvements. Overcoming these obstacles is crucial for success.
How Can Organizations Ensure Sustainability and Continuous Improvement With Six Sigma Metrics and Formulas?
To ensure sustainability and continuous improvement with Six Sigma metrics and formulas, you must prioritize regular monitoring, feedback integration, and team involvement. Embrace a culture that values data-driven decisions and ongoing optimization efforts.
Are There Any Industry-Specific Best Practices for Using Six Sigma Metrics and Formulas Effectively?
To use Six Sigma metrics and formulas effectively in your industry, consider adopting best practices tailored to your sector. By customizing tools and approaches, you can optimize performance, drive continuous improvement, and achieve sustainable results.
How Can Organizations Measure the ROI of Implementing Six Sigma Metrics and Formulas in Their Operations?
To measure the ROI of implementing Six Sigma metrics and formulas in your operations track cost savings, revenue growth, and improved efficiencies. Analyze data before and after implementation to quantify the impact and make informed decisions.
Related Term | Definition |
---|---|
Corporate Training | A program designed to educate employees on various skills and knowledge relevant to their job roles and the company’s objectives. |
Grievance Redressal | A system or process used by an organization to address complaints and resolve disputes raised by employees or customers. |
Root Cause | The fundamental reason for the occurrence of a problem or defect, identifying which can help in preventing future issues. |
Systems Design | The process of defining the architecture, components, modules, interfaces, and data for a system to satisfy specified requirements. |
Development Course | A structured educational or training program focused on improving specific skills or knowledge in a particular field. |
Measure Analyze | A phase in problem-solving and process improvement methodologies where data is collected and analyzed to identify the root cause of problems. |
Six Sigma Techniques | A set of quality management tools and strategies aimed at improving business processes by greatly reducing the probability that an error or defect will occur. |
Python Certification Training | Educational courses designed to teach Python programming skills and prepare individuals for certification exams. |
Data Science with Python | An educational or training program focused on teaching data science principles and techniques using the Python programming language. |
CSM Certification | Refers to Certified ScrumMaster certification, a course and evaluation related to agile project management and scrum practices. |