Six Sigma explained in simple terms, explains the mysteries of a methodology that has redefined excellence in businesses worldwide. Six Sigma, a beacon of efficiency and quality, offers a compelling blueprint for organizations aiming to master their existing processes through the rigorous application of statistical analysis and a deep commitment to continual improvement. By distilling the essence of Six Sigma into accessible insights, this piece serves as a guide for anyone—from upper management to the newest team member—looking to enhance their understanding and application of these principles.
Read more about Six Sigma Explained in Simple Terms
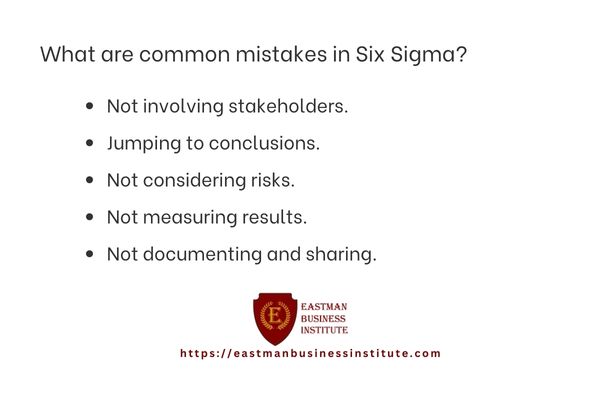
Embark on a journey through the intricacies of process maps, Six Sigma processes, and the coveted Six Sigma black belt, all simplified for clarity and practical application.
Ready to transform the current processes and elevate the organization? Let’s explore how Six Sigma can pave the way for innovation and excellence.
More Things To Know About Six Sigma Explained in Simple Terms
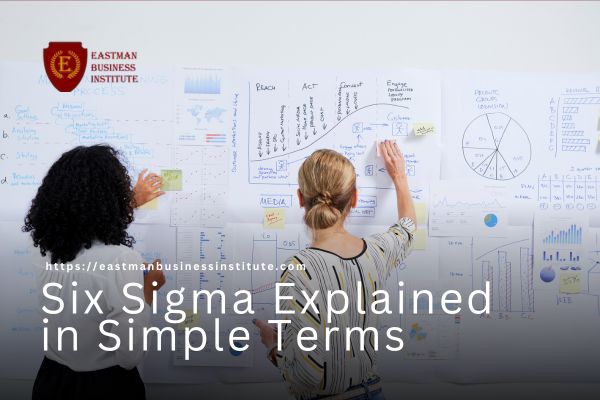
Understanding Six Sigma
Understanding Six Sigma involves grasping its fundamental goal of reducing defects in processes to enhance overall quality. Six Sigma is a methodology that aims to improve the quality of process outputs by identifying and removing the causes of defects and minimizing variability in manufacturing and business process management to achieve a Six Sigma level of quality.
The Six Sigma definition is rooted in statistical methods and a structured approach, with the goal of achieving a level of quality where the probability of a defect occurring is extremely low, at about 3.4 defects per million opportunities.
Implementing a Six Sigma program involves rigorous training, data-driven decision-making, and a focus on continuous improvement to drive efficiency and customer satisfaction. Embracing the principles of Six Sigma can lead to significant improvements in organizational performance and profitability.
History and Evolution of Six Sigma
The evolution of Six Sigma began with its introduction by Motorola in the mid-1980s, marking a significant milestone in the realm of quality management. Initially developed as a set of statistical methods to improve manufacturing processes and reduce defects, Six Sigma quickly gained recognition for its effectiveness in enhancing overall business performance.
This approach to process improvement has evolved beyond its manufacturing roots and is now widely utilized across various industries, including healthcare, finance, and technology. The history of Six Sigma showcases a continuous refinement of methodologies and tools aimed at reducing variation and maximizing efficiency.
Six Sigma Principles
Six Sigma principles focus on the customer, use data for statistical analysis, and aim for continuous process improvement.
Implement proactive management practices to ensure efficient and effective operations.
Focus on the Customer
To implement Six Sigma successfully, prioritize the customer’s needs and expectations. Customer focus lies at the core of the Six Sigma methodology, emphasizing a relentless pursuit of customer satisfaction. By aligning processes with customer requirements, organizations enhance quality management and drive continuous improvement.
Understanding the voice of the customer is essential for identifying critical areas where improvements can be made to meet or exceed customer expectations. Through data-driven decision-making and a commitment to delivering value to customers, businesses can streamline operations, minimize defects, and foster long-term loyalty.
Embracing a culture that revolves around customer satisfaction not only differentiates companies in the market but also ensures sustained success in today’s competitive landscape.
Data and Statistical Analysis
Utilize data analysis to drive decision-making and enhance quality in Six Sigma methodology.
In the realm of Six Sigma methodologies, statistical analysis plays a crucial role. By employing various Six Sigma tools, such as control charts, regression analysis, and hypothesis testing, you can identify patterns, trends, and root causes of defects within processes. The tools of Six Sigma enable you to quantify the performance of your processes and make informed decisions based on data rather than assumptions.
Understanding the statistical significance of your findings allows you to implement targeted improvements that lead to tangible results. Embracing data-driven approaches in your Six Sigma projects empowers you to achieve higher levels of efficiency, quality, and root cause analysis, processes while striving for perfection in every aspect of your operations.
Process Improvement
Transitioning from data and statistical analysis, you can streamline and optimize your processes through Six Sigma principles of process improvement. By employing Six Sigma methodologies, you focus on enhancing efficiency and quality by eliminating defects and variations in your processes.
Process improvement in Six Sigma involves identifying areas for enhancement, setting measurable goals, and utilizing tools like process mapping and value stream mapping to visualize and analyze workflows. Through the systematic application of Six Sigma principles, you can break down complex processes into manageable steps, pinpoint areas of inefficiency, and implement targeted solutions to drive continuous improvement.
Embracing process improvement within the framework of Six Sigma empowers you to create streamlined, effective processes that deliver consistent results and meet or exceed customer expectations.
Proactive Management
Improve your operational efficiency by proactively managing processes using Six Sigma principles. By embracing Six Sigma or Lean Six Sigma methodologies, you can drive continuous process improvements in the entire organization.
Proactive management involves identifying potential issues before they escalate, ensuring smoother operations and higher-quality outputs. With Six Sigma, you focus on data-driven decision-making, setting specific goals, measuring performance, and making adjustments to achieve desired results.
Lean Six Sigma further enhances this approach by eliminating waste and optimizing processes for maximum efficiency. By integrating these principles into your management style, you can create a culture of continuous improvement and proactive problem-solving, leading to sustained success in meeting customer expectations and organizational objectives.
Key Concepts of Six Sigma
DMAIC Methodology entails Define, Measure, Analyze, and Improve. These key concepts are the foundation of Six Sigma principles, guiding you through a structured approach to problem-solving and process improvement.
Understanding these fundamental elements is crucial for implementing Six Sigma successfully in your organization.
DMAIC Methodology
To effectively implement Six Sigma, you need to apply the DMAIC methodology, which stands for Define, Measure, Analyze, Improve, and Control. This structured approach is crucial in the realm of Six Sigma implementation as it provides a roadmap for process improvement.
The DMAIC methodology is at the core of the Six Sigma process, guiding you through the steps necessary to identify areas for enhancement, measure existing processes, analyze data to pinpoint issues, implement improvements, and establish controls to sustain the improvements over time.
DMADV Methodology
To ensure the sustained success of Six Sigma projects, maintaining control through the DMADV Methodology is crucial for achieving long-term performance improvements.
The DMADV Methodology stands for Define, Measure, Analyze, Design, and Verify. This structured approach is used to create new processes, products, or services that meet customer requirements and result in significant quality improvements.
By following the DMADV process, you can identify opportunities for innovation, reduce defects, and enhance overall efficiency. The key concepts of the DMADV Methodology help ensure that the final output exceeds or meets customer expectations.
Applying this method within the Six Sigma framework allows organizations to proactively address potential issues and deliver high-quality solutions consistently.
Six Sigma Roles and Responsibilities
Let’s break down the key roles in Six Sigma:
- Champions lead the initiative.
- Master Black Belts provide guidance and expertise.
- Black Belts focuses on project execution.
- Green Belts assist in projects.
- Yellow Belts support improvement efforts.
Understanding these distinct roles and responsibilities is crucial for the successful implementation of Six Sigma methodologies in your organization. Each role plays a vital part in driving process improvement and achieving measurable results.
Champions
Champions play a crucial role in leading and supporting Six Sigma projects within an organization. They’re key individuals who drive the implementation and success of the Six Sigma program. Champions provide strategic direction, allocate necessary resources, and remove any obstacles that may hinder project progress.
These individuals have a strong understanding of business processes and lean manufacturing principles. They work closely with Black Belts to identify improvement opportunities, set project goals, and ensure alignment with organizational objectives.
Champions serve as advocates for Six Sigma methodologies, promoting a culture of continuous improvement throughout the company. Their active involvement and support are instrumental in achieving significant results and driving positive change in the organization’s performance. Their belt certification underscores their proficiency and commitment to the Six Sigma principles.
Master Black Belts
The Six Sigma Master Black Belt plays a critical role in overseeing project execution and coaching Green and Black Belts. These individuals are experts in the methodology of Six Sigma and are responsible for driving continuous improvement within an organization.
Master Black Belts typically operate at a high sigma level, indicating a deep understanding of statistical tools and techniques. They provide guidance and mentorship to Green and Black Belts, helping them navigate complex projects and achieve significant results.
Master Black Belts often leads strategic initiatives, working closely with Champions to align Six Sigma projects with organizational goals. Their expertise and leadership are essential in ensuring the success of Six Sigma initiatives and driving performance improvement across the organization.
Black Belts
To excel as a Black Belt in Six Sigma, one must demonstrate expertise in statistical analysis and project management. Black Belt’s role is crucial in leading process improvement projects within an organization. Your proficiency in Six Sigma methodologies, combined with your leadership skills, is essential for driving change and ensuring quality enhancement.
Black Belts undergo rigorous training to master the tools and techniques needed to identify root causes of problems and implement effective solutions. Responsibilities include coaching Green Belts, collaborating with stakeholders, and achieving measurable results that align with business objectives.
Embrace the challenge of being a Black Belt in Six Sigma, where your ability to analyze data and manage projects will make a significant impact on organizational success.
Green Belts
Green belt’s role is crucial in driving process improvement initiatives within the framework of Six Sigma methodologies. They play a vital part in quality management by applying Six Sigma tools and techniques to analyze and solve problems, identify inefficiencies, and streamline processes.
Responsibilities include actively participating in project teams, collecting and analyzing data, implementing solutions, and ensuring sustainable improvements. By utilizing Six Sigma knowledge and skills, they can help enhance the overall efficiency, quality, and effectiveness of processes in your organization, ultimately contributing to its success in meeting customer needs and achieving operational excellence.
Yellow Belts
Yellow Belt in Six Sigma support process improvement projects by assisting in data collection and analysis. Yellow Belts are crucial team members who work alongside Green and Black Belts to help streamline processes and enhance overall efficiency.
While Green Belts focuses on leading projects and Black Belts on managing them, Yellow Belts plays a vital role in executing specific tasks within the project scope. With a Yellow Belt certification, you’re equipped to identify opportunities for improvement, gather relevant data, and contribute to the overall success of the project.
Understanding of Six Sigma methodologies and commitment to process improvement make you an essential asset to the team.
Benefits of Implementing Six Sigma
When implementing Six Sigma, expect improved quality in the products or services, leading to increased customer satisfaction.
See reduced costs and waste, which contributes to enhanced operational efficiency.
These benefits of Six Sigma can help your organization streamline processes and achieve higher levels of performance.
Improved Quality of Products or Services
Implementing Six Sigma can lead to a significant reduction in defects, ultimately continually improving the quality of your products or services. By implementing the principles of Six Sigma, you can streamline processes, identify and eliminate errors, and enhance overall quality. This focus on quality not only reduces defects but also leads to improved customer satisfaction.
Six Sigma emphasizes process improvement and empowers organizations to deliver products and services that meet or exceed customer expectations consistently. Through the systematic approach of Six Sigma, you can ensure that your offerings are of high quality, reliable, and tailored to customer needs.
This commitment to quality can set you apart in the market, build customer loyalty, and drive long-term success.
Increased Customer Satisfaction
By focusing on quality improvements through Six Sigma, you can enhance customer satisfaction and loyalty, driving long-term success in your business. Six Sigma’s emphasis on process improvement ensures that your customers receive consistent, high-quality products or services. This consistency leads to increased customer satisfaction as they experience fewer defects or errors in what you offer.
Happy customers are more likely to become repeat buyers and recommend your business to others, thus expanding your customer base. Implementing Six Sigma not only enhances the quality of what you deliver but also creates a positive customer experience, ultimately fostering loyalty and trust in your brand.
Reduced Costs and Waste
To achieve reduced costs and eliminate waste through Six Sigma, streamline processes and eliminate inefficiencies in the operations. By implementing Six Sigma methodologies, you can pinpoint areas where costs are inflated due to errors or unnecessary steps.
This approach enables you to enhance operational efficiency, reduces waste, and lower expenses. Through the rigorous analysis that Six Sigma promotes, you can identify and rectify bottlenecks or redundancies that contribute to increased costs.
This systematic approach not only helps in cutting down expenses but also leads to a more streamlined and effective workflow. Embracing Six Sigma principles empowers you to optimize the processes, maximize resources, and drive significant savings while enhancing the overall performance of your operations.
Enhanced Operational Efficiency
Streamlining processes and eliminating inefficiencies with Six Sigma not only reduces costs and waste but also enhances your operational efficiency significantly.
By implementing Six Sigma methodologies, you can achieve higher levels of operational efficiency through systematic process improvement and effective quality management practices.
Six Sigma enables you to identify and address areas of inefficiency, leading to streamlined workflows, optimized resource utilization, and improved overall productivity.
This approach empowers your organization to deliver products and services more efficiently, meeting customer expectations with higher-quality outputs.
Through the rigorous application of Six Sigma principles, you can drive continuous improvement, enhance operational effectiveness, and establish a culture of excellence within your operations.
Embrace Six Sigma to unlock the full potential of your operational efficiency.
Challenges and Criticisms of Six Sigma
You may encounter challenges when implementing Six Sigma, such as resistance to change or difficulty in sustaining improvements.
Common criticisms include the perception of Six Sigma as a rigid methodology that stifles creativity or focuses too much on data.
It’s essential to address these criticisms by fostering a culture that values innovation alongside process improvement.
Potential Drawbacks
Facing resistance from some stakeholders, implementing Six Sigma may present challenges in organizations striving for process improvement. One potential drawback is the difficulty in aligning Six Sigma methodologies with evolving customer expectations. This mismatch can hinder the effectiveness of process improvement efforts.
Some critics argue that Six Sigma’s heavy reliance on statistical analysis and data-driven decisions may overlook qualitative aspects crucial to customer satisfaction. To address these challenges, organizations can consider incorporating qualitative feedback alongside quantitative data in their Six Sigma projects.
Conducting a comprehensive financial analysis to measure the impact of Six Sigma initiatives on the bottom line can help justify investments and demonstrate the value of process improvement efforts.
Common Misconceptions
When diving into Six Sigma, be mindful of common misconceptions surrounding its challenges and criticisms. One prevalent misunderstanding is that obtaining a white belt or black belt in Six Sigma means you’re an expert. In reality, these belts signify different levels of training and proficiency, not mastery, emphasizing the importance of rigorous Six Sigma training.
Another misconception is that Six Sigma is solely for manufacturing industries. While it originated in manufacturing, Six Sigma principles can be applied across various sectors like healthcare, finance, and service industries.
Some critics argue that Six Sigma is too rigid and that it stifles creativity and innovation. When implemented correctly, Six Sigma can actually enhance problem-solving and decision-making processes by providing a structured approach to improvement.
Addressing the Criticisms
Addressing critiques and skepticism surrounding Six Sigma is crucial for understanding its true value and potential impact. To overcome criticisms, it’s essential to have a deep understanding of the Six Sigma methodology.
One common critique is that Six Sigma can be too rigid, focusing excessively on meeting quality standards at the expense of innovation. During the improvement phase of Six Sigma, innovation is encouraged alongside quality improvements.
Another criticism is that Six Sigma may not be suitable for every type of organization or project. While it may not be a one-size-fits-all solution, adapting Six Sigma principles to fit the specific needs and goals of an organization can enhance its effectiveness and relevance.
Future of Six Sigma
As we look ahead to the future of Six Sigma, consider the evolving landscape of Industry 4.0 and how Six Sigma can adapt to the challenges and opportunities it presents.
With the integration of Artificial Intelligence, Six Sigma methodologies may become even more precise and efficient, revolutionizing quality control processes.
In a post-pandemic world, the role of Six Sigma in ensuring resilience and adaptability within organizations is likely paramount.
Six Sigma and Industry 0
As we delve into the future of Six Sigma, it becomes evident that Industry 0 will play a critical role in shaping its evolution. Industry 0, also known as the future phase beyond Industry 4.0, focuses on the integration of cyber-physical systems into manufacturing processes.
Six Sigma and Industry 0 will revolutionize process improvement methodologies within the manufacturing industry. By combining the principles of Six Sigma with the advancements of Industry 0, companies can achieve enhanced efficiency, reduced defects, and optimized production processes. This collaboration will lead to smarter factories that utilize real-time data analytics, automation, and interconnected systems to drive continuous improvement.
Embracing Industry 0 alongside Six Sigma will be pivotal for organizations aiming to stay competitive and innovative in the rapidly evolving manufacturing landscape.
Six Sigma and Artificial Intelligence
Continuing from Industry 0, you’ll discover how Six Sigma integrates with artificial intelligence to drive further advancements in process improvement methodologies within manufacturing. By combining Six Sigma principles with artificial intelligence capabilities, organizations can enhance project management, streamline process improvement initiatives, and elevate total quality management practices.
Artificial intelligence tools can analyze vast amounts of data to identify patterns, predict potential issues, and optimize processes in real time, aligning perfectly with the goals of Six Sigma methodologies. This integration enables quicker decision-making, more accurate problem-solving, and a proactive approach to quality control.
As technology continues to evolve, the fusion of Six Sigma, artificial intelligence, and value stream holds immense potential to revolutionize how businesses achieve operational excellence and sustainable growth.
The Role of Six Sigma in a Post-Pandemic World
Embrace the future of Six Sigma in a post-pandemic world by adapting to new challenges and opportunities.
The role of Six Sigma in a post-pandemic world is crucial for organizations aiming to enhance the quality of products and services. By applying the knowledge gained from Six Sigma, which is explained in simple terms, businesses can engage in continuous process improvement to meet evolving customer needs efficiently.
Post-pandemic, the focus on quality has become even more paramount as customer expectations shift. Six Sigma provides a structured approach to streamline operations, reduce errors, and optimize resources.
Embracing Six Sigma in this new landscape won’t only drive operational excellence but also foster resilience and competitiveness in a rapidly changing world.
Frequently Asked Questions
Can Six Sigma Be Applied in Industries Other Than Manufacturing?
Yes, Six Sigma can be applied in various industries beyond manufacturing. Its principles of process improvement, data-driven decision-making, and reducing defects are adaptable to sectors like healthcare, finance, and service-oriented businesses for quality improvement.
How Long Does It Typically Take to See Significant Results From Implementing Six Sigma?
Typically, you’ll start seeing significant results from implementing Six Sigma within a few months. By focusing on data-driven improvements and eliminating defects, your organization can experience positive changes relatively quickly.
What Are Some Common Misconceptions About Six Sigma?
Common misconceptions about Six Sigma include it being only for large companies, requiring specialized training, and being a quick fix solution. It can benefit organizations of all sizes and is a long-term improvement strategy.
How Does Six Sigma Differ From Other Quality Management Methodologies, Such as Lean or TQM?
Six Sigma focuses on reducing defects and variations, emphasizing statistical analysis and process improvement. Lean aims to eliminate waste and enhance efficiency. TQM prioritizes customer satisfaction through continuous quality enhancement. Each methodology offers unique approaches to quality management.
Are There Any Specific Industries or Organizations That Are Not Well-Suited for Implementing Six Sigma?
In some creative or rapidly changing industries, Six Sigma may face challenges due to its structured approach. With adaptation and leadership support, most organizations can benefit from implementing Six Sigma principles effectively.
Glossary of Related Terms | |
---|---|
Related Term | Definition |
Business Strategy | A plan of action designed to achieve a long-term or overall aim within a business, considering internal and external factors. |
Measurement | The process of obtaining the quantitative value of an attribute or phenomenon, typically using instruments and standardized units. |
Normal Distribution | A probability distribution that is symmetric about the mean, showing that data near the mean are more frequent in occurrence than data far from the mean. |
Process Flow | A graphical representation of the steps, activities, and decision points involved in a specific process from start to finish. |
Standard Deviation | A measure of the amount of variation or dispersion of a set of values; a low standard deviation indicates that the values tend to be close to the mean. |
Statistical Process Control | A method of quality control which employs statistical methods to monitor and control a process, helping to ensure that it operates at its full potential. |
Design of Experiments | A systematic method to determine the relationship between factors affecting a process and the output of that process, used to find cause-and-effect relationships. |
Specification Limits | Boundaries or constraints set for the values of process or product measurements, which are used to determine the acceptability of the measurement. |
Balanced Scorecard | A strategic planning and management system used to align business activities to the vision and strategy of the organization by monitoring performance against strategic goals. |
Statistical Processes | Processes that are analyzed and controlled through statistical methods to maintain and improve process quality and performance. |