In the competitive landscape of modern business, efficiency, and innovation are not just goals—they are imperatives. This imperative leads us directly to the DMAIC Model and DMADV Model explained, two cornerstone methodologies of Six Sigma that offer a structured, data-driven blueprint for success.
Whether you’re refining an existing process or designing a new one, these models—DMAIC (Define, Measure, Analyze, Improve, Control) and DMADV (Define, Measure, Analyze, Design, Verify)—are essential tools. By implementing these Sigma methodologies, organizations can enhance customer satisfaction, improve employee engagement, and achieve their primary objectives with unparalleled precision.
Read more about The DMAIC Model and DMADV Model Explained

Let’s dive into how these strategies can be systematically applied to transform your business process and achieve enduring excellence.
More Things To Know About The DMAIC Model and DMADV Model Explained
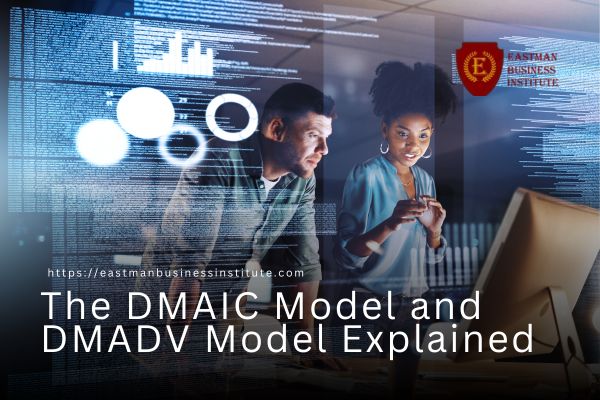
Understanding the DMAIC Model
To understand the DMAIC Model, it’s essential to grasp its structured approach to problem-solving. DMAIC stands for Define, Measure, Analyze, Improve, and Control. This methodology is a key component of the Six Sigma process improvement strategy widely used in various industries.
It involves a systematic analysis of business processes to identify areas for improvement. Through the use of control charts and data analysis techniques, the DMAIC Model helps organizations pinpoint inefficiencies and implement targeted solutions. By focusing on data-driven decision-making and continuous improvement, companies can streamline operations, enhance quality, and achieve sustainable results.
Embracing the DMAIC Model empowers teams to tackle challenges proactively and drive positive change within their organizations.
The Five Phases of the DMAIC Model
Moving on to the Five Phases of the DMAIC Model, understanding each step is important for successfully implementing this structured problem-solving approach.
The DMAIC model consists of five key phases: Define, Measure, Analyze, Improve, and Control.
In the Define phase, you’ll outline the project goals and identify customer requirements.
The Measure phase involves quantifying the current process performance.
Next, in the Analyze phase, you’ll dig deep into the data to uncover root causes of issues.
Once the problems are understood, the Improve phase focuses on implementing solutions to enhance the process.
Finally, the Control phase guarantees that the improvements made are sustained over time.
Mastering these phases is essential for effective improvement using the DMAIC model.
Define Phase
Understanding the Define Phase in the DMAIC Model is important for setting clear project goals and identifying customer requirements. During this phase, it’s essential to gather and analyze information related to customer requirements, process capability, and quality control. Data collection plays a significant role in defining the project scope and objectives.
Identifying the root cause of the issue at hand is a key aspect of the Define Phase. By clearly understanding customer needs and expectations, you can establish a solid foundation for the improvement project.
Ensuring that all stakeholders are aligned on the project goals and requirements is essential to proceed effectively into the next phases of the DMAIC Model.
Measure Phase
As we progress from defining project goals and customer requirements in the Define Phase, shift our focus to quantifying process performance and gathering data in the Measure Phase of the DMAIC Model.
In this phase, we’ll establish process controls, define metrics to measure performance and collect relevant data to assess the current state of the process. By analyzing this data, we can identify areas for improvement and determine the extent of performance gaps.
The Measure Phase is essential for setting a baseline of the process’s current performance, which will serve as a reference point for evaluating the effectiveness of any changes made in the subsequent stages of the DMAIC Model.
Analyze Phase
In the Analyze Phase of the DMAIC Model, you’ll investigate thoroughly the data collected during the Measure Phase to identify patterns, root causes, and potential solutions for process improvement. This phase is critical for understanding the current state of the process.
By utilizing statistical tools and quantitative tools, you can explore the data to uncover trends and relationships that may not have been initially apparent. The goal of the Analyze Phase is to pinpoint areas where improvements can be made, leading to enhanced efficiency and effectiveness.
Improve Phase
As we progress from the Analyze Phase to the Improve Phase in the DMAIC Model, our focus shifts towards implementing targeted solutions identified through data analysis.
This phase is crucial in the improvement process as it involves making changes to existing processes to achieve better outcomes. By analyzing data collected during the previous steps, you can pinpoint areas that require enhancement and develop strategies for incremental improvements.
The Improve Phase is where the proposed solutions are put into action, often involving process design modifications. It’s essential to closely monitor these changes to make sure they’re leading to the desired results, setting the stage for the upcoming Control Phase.
Control Phase
Guarantee effective management and sustainability of improvements by incorporating the Control Phase in the DMAIC Model.
In this phase, the focus shifts towards maintaining the gains achieved during the Improve Phase. By implementing control processes, you make sure that the improved methods become part of the existing process and are consistently followed.
It’s essential to identify the root cause of any deviations from the desired outcomes and put measures in place to address them promptly. This phase aims to establish a system that can both improve existing processes and control them effectively.
Through continuous monitoring and adjustment, you can make certain that the improvements made are sustained over time.
Applications of the DMAIC Model
Maintain effective management and sustain improvements by applying the DMAIC Model through its various applications. The DMAIC Model is a structured approach used in improvement projects to enhance processes and increase customer satisfaction.
Here are some key applications of the DMAIC Model:
- Identifying Problems: Use the DMAIC Model to systematically identify issues affecting performance.
- Analyzing Data: Analyze data to understand the root causes of problems and make informed decisions.
- Implementing Solutions: Develop and implement solutions to address identified issues effectively.
- Monitoring Progress: Continuously monitor progress to guarantee sustained improvements and meet customer satisfaction goals.
Benefits of Using the DMAIC Model
Maximize the full potential of your improvement projects by leveraging the DMAIC Model’s numerous benefits. By following DMAIC, you can align your processes with customer specifications, ensuring their needs are met effectively.
Continuous improvement is at the core of DMAIC, allowing you to enhance operations incrementally. The model empowers you to reduce variations in your processes, leading to higher-quality outcomes. Implementing DMAIC within your organization can drive lean Six Sigma practices, streamlining operations and minimizing waste.
Whether you’re improving an existing process or tackling a new challenge, DMAIC provides a structured approach to problem-solving and achieving sustainable results. Embrace the benefits of DMAIC to enhance efficiency and drive success in your projects.
Understanding the DMADV Model
When exploring the DMADV model, you’ll first encounter its definition and the five important phases it entails.
The Define Phase, Measure Phase, and Analyze Phase are fundamental components of this structured approach.
Familiarizing yourself with each stage will lay a solid foundation for comprehending the DMADV model in its entirety.
Definition of DMADV Model
The DMADV model, also known as Define, Measure, Analyze, Design, Verify, is a structured approach used to create new processes or products with high levels of success and efficiency. DMAD methodology is particularly focused on the design phase of product development, ensuring that the final product designs meet or exceed customer expectations.
By following a structured approach like DMADV, companies can systematically innovate and develop products that aren’t only efficient but also align closely with what customers desire. This methodical process helps in reducing errors, enhancing quality, and achieving customer satisfaction.
The DMADV model serves as a guide for organizations to navigate through the complexities of designing new products that are tailored to meet specific customer needs.
The Five Phases of DMADV Model
To understand the DMADV model fully, it’s imperative to grasp the five distinct phases that form the backbone of this structured approach to product development.
The first phase is about defining the design concept, setting the stage for the project. Following that, the high-level design stage involves outlining the initial specifications and requirements.
The third phase focuses on identifying the root cause of any potential issues or inefficiencies. Moving on, the finished design phase refines the design based on feedback and testing, ensuring it meets all necessary criteria.
Define Phase
Understanding the essence of the Define Phase in the DMADV model is critical for effective product development. This initial phase sets the groundwork by clearly defining the project goals, customer requirements, and the scope of the project.
During this stage, you’ll define the processes that need improvement, establish measurement systems, and identify critical-to-quality parameters. By defining the project scope and objectives, you pave the way for a successful design phase.
It’s essential to involve key stakeholders and gather their input to guarantee alignment with customer expectations. Successful completion of the Define Phase provides a solid foundation for the subsequent measure, analysis, design, and verification phases in the DMADV model.
Measure Phase
Why is the Measure Phase important in the DMADV model for effective product development?
The Measure Phase plays a vital role in understanding key metrics, establishing a baseline, and aligning the project with customer demands.
During this phase, you’ll identify the essential parameters that need to be measured to assess the current state accurately.
By setting up simulations and collecting relevant data, you can gain insights into the performance of the existing processes or products.
This step allows you to quantify the gap between the current situation and the desired outcome, providing a clear understanding of what needs to be improved or developed to meet customer expectations effectively.
Analyze Phase
Exploring the Analyze Phase in the DMADV model reveals important insights into the project’s data and facilitates informed decision-making for product development. In this phase, utilizing the Six Sigma methodology, Green Belts plays an important role in analyzing the data to identify key patterns and trends.
One important tool used during this phase is the Pareto chart, which helps in prioritizing issues based on their impact. Qualitative tools such as interviews, surveys, and focus groups are employed to gather subjective data that complements the quantitative analysis.
Design Phase
To proceed effectively from the Analyze Phase to the Design Phase in the DMADV model, you’ll shift focus towards creating innovative solutions based on the insights gained from data analysis.
In the Design Phase, you’ll utilize your green belt certifications to develop a detailed plan for the new product or process. This phase involves creating a flow chart to map out the steps needed to bring your design to life.
Unlike DMAIC, which focuses on improving an existing product or process, DMADV is geared towards designing and verifying a new product or process. Understanding the differences between DMAIC and DMADV is essential as you move forward in the improvement process.
Verify Phase
In the Verify Phase of the DMADV model, you’ll validate the design of the new product or process to guarantee it meets the established criteria for success. This phase focuses on ensuring that the newly developed processes are thoroughly tested through pilot runs.
By conducting these pilot runs, you can gather essential data to create accurate baselines for performance evaluation. Involving the customer service team during this phase is important. Their feedback and insights can help confirm if the new processes align with customer needs and expectations.
Verifying the design at this stage is important to identify any potential issues early on and make necessary adjustments before full implementation.
Applications of DMADV Model
As you consider the Applications of the DMADV Model, it’s important to understand how this model can be effectively utilized in various industries to drive successful project outcomes.
The DMADV model, with its focus on creating new processes or products that meet customer requirements, can be a powerful tool for achieving business goals.
Some key applications of the DMADV model include:
- Developing new products or services that align with customer requirements
- Implementing improvement methods to enhance existing processes
- Ensuring that projects are geared towards achieving specific business goals
- Streamlining operations by optimizing processes to meet customer needs
Benefits of Using the DMADV Model
Utilizing the DMADV model offers businesses a structured approach to innovating processes and products that directly align with customer needs. The benefits of using the DMADV model include a focus on design activities from the start, ensuring that the final product or process meets customer requirements and expectations.
By incorporating the DMADV model, businesses can achieve maximum customer satisfaction by proactively addressing customer needs during the design phase. This model allows companies to create robust designs that are tailored to customer preferences, leading to improved product quality and increased customer loyalty.
Comparing DMAIC and DMADV Models
When comparing DMAIC and DMADV models, you’ll notice several similarities that underline their structured problem-solving approach. The key differences in their application and focus areas will help you decide which model suits your project best.
Understanding these distinctions is essential for making an informed choice between DMAIC and DMADV methodologies.
Similarities Between DMAIC and DMADV Models
Comparing the DMAIC and DMADV models reveals key similarities in their structured problem-solving approaches. Both DMAIC and DMADV methodologies share a focus on improving processes within an organization. One significant similarity between the two is their emphasis on data-driven decision-making. In both models, data analysis plays a critical role in identifying issues, understanding root causes, and evaluating potential solutions.
DMAIC and DMADV prioritize the involvement of cross-functional teams to leverage diverse perspectives and expertise in problem-solving. This collaborative approach fosters innovation and guarantees thorough solutions to complex problems. By following either of these models, organizations can systematically address challenges, drive continuous improvement, and achieve sustainable results.
Differences Between DMAIC and DMADV Models
To differentiate between the DMAIC and DMADV models, consider their distinct stages and objectives. When comparing DMAIC vs. DMADV, notable differences become evident. DMAIC focuses on improving existing processes by identifying and resolving common quality issues, while DMADV emphasizes creating new processes with a strong emphasis on detailed design. The table below highlights some key variances between the two models:
Aspect | DMAIC | DMADV |
---|---|---|
Goal | Improve existing processes | Create new processes |
Approach | Reactive | Proactive |
Focus | Problem-solving and optimization | Innovation and design |
Understanding these differences can help you choose the most suitable model for your project based on its specific needs and objectives.
Choosing Between DMAIC and DMADV Models
Consider the specific needs and objectives of your project when deciding between the DMAIC and DMADV models.
The DMAIC methodology is suitable when you aim to improve an existing process, focusing on identifying issues, analyzing data, and implementing solutions through defined stages: Define, Measure, Analyze, Improve, and Control.
The DMADV process is more fitting when you’re working on designing a new product or process, with stages that include Define, Measure, Analyze, Design, and Verify.
The key differences lie in the focus on improvement versus design, making it important to choose the model that aligns best with your project goals and requirements.
Evaluate these distinctions carefully to select the most appropriate approach for your specific situation.
Real-world Applications and Success Stories
You’ll explore successful implementations of both the DMAIC and DMADV models in various industries.
Discover how organizations have applied these methodologies to achieve significant improvements in processes and outcomes.
Gain insights into the lessons learned from these real-world applications to enhance your understanding of quality management practices.
Successful Implementations of the DMAIC Model
In real-world scenarios, successful implementations of the DMAIC model have revolutionized processes and yielded impressive results. Whether led by a Green Belt, Lean Six Sigma Black Belt, or through Lean Continuous Improvement initiatives, organizations have seen significant improvements in efficiency, quality, and customer satisfaction.
For example, a manufacturing company applied the DMAIC model to streamline its production line, resulting in a 30% reduction in defects and a 20% increase in productivity within six months. By identifying root causes, implementing data-driven solutions, and continuously monitoring progress, businesses across various industries have harnessed the power of DMAIC to drive sustainable change and achieve measurable success.
Successful Implementations of DMADV Model
Successful implementations of the DMADV model have demonstrated remarkable achievements in various industries, showcasing the model’s effectiveness in driving innovation and excellence.
Companies that have embraced the DMADV approach have successfully created new processes that are more efficient, cost-effective, and customer-centric. For example, a leading electronics manufacturer utilized the DMADV model to redesign its product development process, resulting in a significant decrease in time-to-market and an increase in product quality.
In another instance, a healthcare organization applied the DMADV principles to enhance its patient care delivery, leading to improved patient outcomes and higher satisfaction rates. These success stories highlight the power of the DMADV model in guiding organizations through a structured design process that focuses on delivering superior results.
Lessons Learned from These Implementations
Through real-world applications and success stories, valuable lessons have been gleaned from the implementations of the DMADV model. By studying these cases, you can learn from the lessons learned and apply them to your current processes.
Understanding how organizations have leveraged the DMADV model can help you make informed decisions when faced with similar opportunities. These implementations showcase the power of following a structured approach to design and innovate products or services.
Frequently Asked Questions
What Are the Key Differences Between the DMAIC and DMADV Models in Terms of Their Overall Approach and Purpose?
When comparing the DMAIC and DMADV models, focus on their distinct approaches and purposes. DMAIC is for process improvement, while DMADV is for designing new processes. Understand these differences to apply the right method effectively.
How Can Organizations Effectively Decide Whether to Use the DMAIC or DMADV Model for a Specific Project or Process Improvement Initiative?
To effectively decide on using DMAIC or DMADV, assess project goals and complexity. Choose DMAIC for process improvement with existing systems and DMADV for new projects. Consider timelines, resources, and desired outcomes for best fit.
Are There Any Common Challenges or Pitfalls That Organizations Encounter When Implementing Either the DMAIC or DMADV Model?
When implementing either the DMAIC or DMADV model, you may encounter common challenges like resistance to change, lack of stakeholder buy-in, poor data quality, scope creep, and inadequate resources. Proper planning and communication can help navigate these issues effectively.
How Do Organizations Typically Measure the Success and Effectiveness of Their Implementation of the DMAIC or DMADV Model?
To measure success, you assess project outcomes against set goals, monitor process improvements, gather feedback from stakeholders, and track key performance indicators. Regularly review data, conduct post-implementation audits, and adjust strategies as needed.
Can the DMAIC and DMADV Models Be Used in Conjunction With Each Other, or Are They Typically Applied Separately in Different Scenarios?
Yes, you can use the DMAIC and DMADV models together to complement each other’s strengths. They are not strictly applied separately. Leveraging both can lead to thorough problem-solving and innovation in various organizational scenarios.
Related Term | Definition |
---|---|
Business model | A framework for creating economic, social, and/or other forms of value. It outlines how a company creates, delivers, and captures value, in economic, social, cultural, or other contexts. |
Collecting data | The process of gathering information to analyze and make decisions. This can be quantitative or qualitative data collected through various methods like surveys, observations, or using technology. |
DMADV methodology | A data-driven quality strategy for designing products and processes, it stands for Define, Measure, Analyze, Design, and Verify. |
DMAIC process | A systematic, data-driven methodology used to improve existing business processes. The acronym stands for Define, Measure, Analyze, Improve, and Control. |
Employee satisfaction | The level of contentment and positive perception an employee has with their job and work environment, which can influence productivity and company culture. |
New process | Introduction or implementation of a new set of procedures or workflows in a business to improve efficiency or address specific challenges. |
Analyze improve and control | Part of the DMAIC process; involves using data to identify problems (Analyze), implement solutions (Improve), and establish controls to sustain gains (Control). |
Black belts | Individuals certified in Six Sigma methodologies who lead project teams and are responsible for implementing process improvements. |
Boot camp | An intensive, short-term training program where individuals are immersed in learning about specific subjects or skills, often related to business or technology. |
Collecting data | The process of gathering information to analyze and make decisions. This can be quantitative or qualitative data collected through various methods like surveys, observations, or using technology. |