Understanding how Six Sigma methodology works is key to unlocking unparalleled efficiency and quality in business processes in today’s competitive landscape. Originating from the visionary insights of Bill Smith and embraced by upper management across industries, Six Sigma represents a pinnacle of process optimization.
It goes beyond mere defect reduction, integrating statistical methods and a robust management system to elevate operations. This methodology is not just about minimizing errors; it’s a comprehensive approach that spans from the Six Sigma White Belt to the Lean Six Sigma Green Belt, aimed at enhancing customer satisfaction and operational excellence. Through statistical analysis, including normal distribution and standard deviation, Six Sigma practitioners analyze, improve, and control processes, thereby increasing efficiency and setting new standards of excellence.
Read more about How Six Sigma Methodology Works
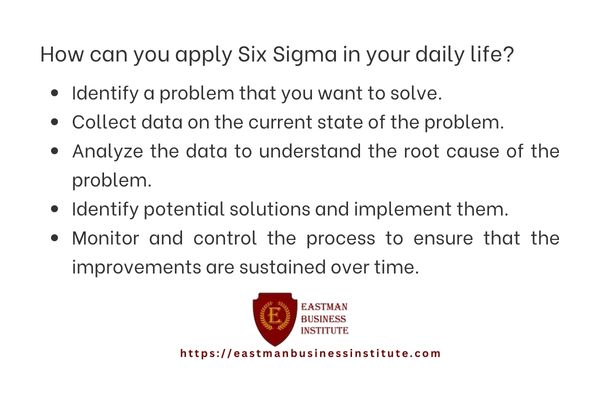
As we delve into this article, we will uncover the transformative power of Six Sigma and how it can significantly improve business processes, ensuring that organizations achieve and sustain peak performance.
More Things To Know About How Six Sigma Methodology Works
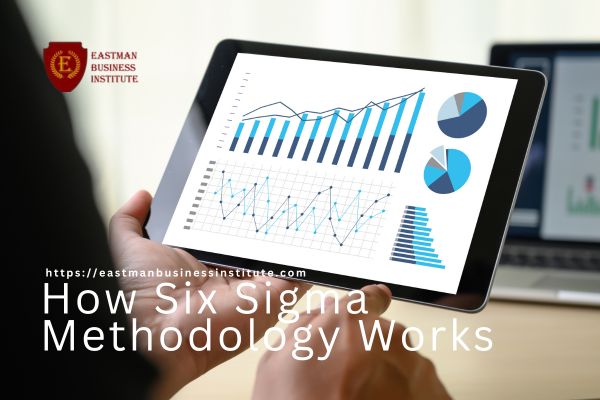
Understanding Six Sigma
Six Sigma is a data-driven methodology that aims to improve processes by identifying and removing defects or variations. At its core, Six Sigma is focused on achieving near-perfection by reducing the number of defects to 3.4 per million opportunities.
The key principles of Six Sigma include a customer-centric approach, process improvement through DMAIC (Define, Measure, Analyze, Improve, Control), and a focus on data-driven decision-making.
Six Sigma tools such as process mapping, root cause analysis, and statistical analysis are used to identify areas for improvement and measure progress accurately.
Understanding these foundational aspects of Six Sigma is essential for successfully implementing the methodology in any organization.
History and Evolution of Six Sigma
Six Sigma methodology traces back to the 1980s at Motorola, where it was developed to enhance quality control processes.
Over time, companies like General Electric embraced and popularized Six Sigma, leading to its widespread adoption across industries. The evolution of Six Sigma has seen it evolve from a quality control tool to a comprehensive business strategy focused on continuous improvement and customer satisfaction.
Obtaining a Six Sigma certification has become a valuable asset for professionals seeking to demonstrate expertise in process improvement and problem-solving. Understanding the history and evolution of Six Sigma is crucial for grasping its significance in modern business practices.
Six Sigma Principles
Six Sigma principles revolve around focusing on the customer, utilizing data and statistical analysis, improving processes, and fostering proactive management and collaboration.
These elements serve as the foundation for successful implementation of the Six Sigma methodology in the organization.
Focus on the Customer
One key principle of Six Sigma methodology is ensuring that customer needs and expectations are at the forefront of all processes. Customer focus is paramount in Six Sigma methodology, where understanding customer requirements and striving for customer satisfaction are central.
By placing the customer at the core of decision-making processes, organizations can align their strategies to meet and exceed customer expectations. This approach not only leads to improved customer satisfaction but also helps in driving business success.
Through the Six Sigma methodology, businesses can analyze customer feedback, identify areas for improvement, and implement changes that directly impact customer experience. Ultimately, a strong emphasis on customer-centric practices is key to achieving sustainable growth and maintaining a competitive edge in the market.
Data and Statistical Analysis
Utilize data and statistical analysis as foundational pillars in implementing Six Sigma principles effectively.
The essence of the Six Sigma methodology lies in its data-driven approach, where decisions are based on factual information rather than assumptions. Statistical analysis plays a crucial role in identifying the root causes of variations and determining the best course of action to improve processes.
By leveraging six sigma tools such as control charts, regression analysis, and hypothesis testing, you can gain valuable insights into your operations and drive continuous improvement.
Embrace the power of data to enhance decision-making, prioritize areas for optimization, and ultimately achieve higher levels of quality and efficiency within your organization.
Process Improvement
To improve processes effectively using Six Sigma principles, start by identifying key areas for enhancement based on data-driven analysis. Six Sigma methodology emphasizes the importance of streamlining operations to minimize defects and enhance overall efficiency.
By implementing Six Sigma tools such as DMAIC (Define, Measure, Analyze, Improve, Control) or DMADV (Define, Measure, Analyze, Design, Verify), you can systematically address process improvement. The Six Sigma process involves setting clear goals, measuring current performance, analyzing root causes of issues, implementing solutions, and establishing controls to sustain improvements.
Through this structured approach, organizations can achieve higher quality outputs, increased customer satisfaction, and reduced waste. Embrace the principles of Six Sigma to drive continuous improvement and elevate your processes to new levels of excellence.
Proactive Management
Improve operational efficiency by implementing Six Sigma principles for proactive management. In the realm of proactive management, Six Sigma methodology plays a crucial role in driving continuous improvement.
By initiating Six Sigma projects, you can identify areas for enhancement, set measurable goals, and meticulously analyze data to make informed decisions. Proactive management involves staying ahead of potential issues by using Six Sigma training to equip your team with problem-solving tools and quality improvement techniques.
Through proactive management practices rooted in Six Sigma principles, you can streamline processes, reduce defects, and optimize performance across your organization. Stay proactive, stay efficient, and embrace the power of Six Sigma for sustained success.
Collaboration
By collaborating with team members trained in Six Sigma, you can leverage diverse perspectives to drive continuous improvement and achieve operational excellence.
In Six Sigma methodologies, the project team plays a crucial role in implementing quality improvement initiatives. Working together, team members can utilize various Six Sigma tools to analyze processes, identify areas for enhancement, and develop effective solutions.
Collaboration within the project team fosters a culture of shared responsibility and accountability for achieving desired outcomes. Through effective communication and teamwork, individuals can align their efforts towards common goals, ensuring that quality improvement efforts are sustained over time.
Utilizing Six Sigma principles, collaboration becomes a cornerstone for success in driving organizational excellence and delivering value to customers.
Key Components of Six Sigma
When exploring the key components of Six Sigma, you’ll encounter methodologies like DMAIC and DMADV. These serve as structured approaches for process improvement.
Understanding the various roles within Six Sigma is essential for effective implementation. Roles such as Champions, Master Black Belts, Black Belts, Green Belts, and Yellow Belts play crucial parts in the process.
These components work together to streamline processes, reduce defects, and drive continuous improvement within an organization.
DMAIC (Define, Measure, Analyze, Improve, Control)
To effectively implement the Six Sigma methodology, you begin with the DMAIC process. This structured approach consists of five key phases:
- Define: Clearly outline the problem, project goals, and customer requirements.
- Measure: Quantify the current process performance using data and metrics.
- Analyze: Identify root causes of defects or inefficiencies in the process.
- Improve: Implement solutions to address the issues and enhance the process.
DMADV (Define, Measure, Analyze, Design, Verify)
In Six Sigma methodology, the DMADV process, consisting of five stages, guides you through defining, measuring, analyzing, designing, and verifying processes to achieve high-quality outcomes.
Firstly, you’ll define the project goals and customer requirements clearly. Next, you’ll measure and identify critical aspects that require improvement. Then, you’ll analyze data to understand root causes and potential solutions.
After the analysis, you move on to the design phase, where you develop and implement a new process. Finally, the last step is to verify the effectiveness of the new process through testing and pilot runs.
Roles and Responsibilities in Six Sigma (Champions, Master Black Belts, Black Belts, Green Belts, Yellow Belts)
As you transition from understanding the DMADV process in Six Sigma methodology, it’s essential to grasp the key roles and responsibilities that drive successful Six Sigma implementation. In this methodology, roles like Champions, Master Black Belts, Black Belts, Green Belts, and Yellow Belts play vital parts.
Champions are top-level executives responsible for supporting and promoting Six Sigma initiatives. Sigma Master Black Belt is an expert who mentor Black Belts and oversee multiple projects. Black Belts leads projects full-time, focusing on data analysis and implementation. Green Belts assists Black Belts in smaller projects part-time. Lastly, Yellow Belts are team members who support project improvements within their areas.
Understanding these roles and responsibilities is crucial for effective implementation of the Six Sigma methodology.
Six Sigma Tools and Techniques
Let’s explore some fundamental Six Sigma tools and techniques that are crucial for process improvement. Cause and Effect Diagrams, Flowcharts, Control Charts, Histograms, and Pareto Charts are commonly used to analyze and visualize data, identify root causes, and prioritize areas for improvement.
These tools play a vital role in guiding organizations toward achieving higher quality standards and operational efficiency.
Cause and Effect Diagrams
To effectively identify root causes in your processes, start utilizing Cause and Effect Diagrams as a key Six Sigma tool. In the realm of Six Sigma methodology, these diagrams play a vital role in root-cause analysis during a Six Sigma project. By visually mapping out potential factors contributing to a problem or defect, you can systematically analyze and prioritize these causes.
This structured approach aligns with the core principles of Six Sigma quality, emphasizing data-driven decision-making. As you delve into your Six Sigma project, integrating Cause and Effect Diagrams can streamline the identification of critical areas for improvement, ultimately enhancing the efficiency and effectiveness of your processes.
Embrace this powerful tool to drive impactful change and achieve higher levels of quality.
Flowcharts
Utilize flowcharts as a crucial tool for mapping out processes and identifying potential areas of improvement in your Six Sigma projects. In the realm of Six Sigma methodology, flowcharts play a pivotal role in visualizing the flow of processes, making it easier to pinpoint inefficiencies or bottlenecks.
By creating detailed process maps using flowcharts, you can gain a comprehensive understanding of how different steps interconnect and where enhancements are needed to achieve Six Sigma quality. These visual representations not only aid in streamlining processes but also facilitate effective communication within teams working on Six Sigma projects.
Embracing flowcharts as part of your Six Sigma toolkit empowers you to enhance process efficiency and drive continuous improvement initiatives in your organization.
Control Charts
Control charts are vital statistical tools within the Six Sigma methodology that aid in process control. By plotting data points over time and setting control limits, these charts enable you to distinguish between normal process variation and special causes of variation. This differentiation is crucial for identifying when a process is out of control and requires intervention.
Control charts provide a visual representation of process performance, allowing you to make data-driven decisions to maintain stability and meet quality standards. Through the continuous monitoring offered by control charts, you can ensure that your Six Sigma projects remain on track and deliver consistent results.
Histograms
When analyzing data in your Six Sigma projects, it’s essential to use histograms as a visualization tool to understand the distribution of values.
Histograms help you grasp the spread and shape of data, making it easier to identify patterns, anomalies, or areas that require improvement within the Six Sigma methodology.
As a key component of the Six Sigma program, histograms enable you to apply statistical thinking by visually representing data in a way that highlights trends and variations.
Pareto Charts
To effectively analyze data in your Six Sigma projects, it’s crucial to incorporate Pareto Charts as they provide valuable insights into the most significant factors affecting your processes.
Pareto Charts, a key tool in the Six Sigma methodology, help you identify and prioritize the root causes of problems within your processes.
By visually representing the frequency or impact of various issues, Pareto Charts enable you to focus your efforts on the vital few factors that contribute most to defects or inefficiencies.
This strategic approach aligns with the core principles of the Six Sigma method, emphasizing data-driven decision-making and process improvement.
Integrating Pareto Charts into your Six Sigma program enhances your ability to drive impactful changes and achieve measurable results efficiently.
Scatter Diagrams
Incorporate Scatter Diagrams to visually represent relationships between variables in your Six Sigma projects, aiding in further analysis and decision-making. Scatter Diagrams are a vital tool in Six Sigma methodology, assisting in quality management by illustrating the correlation between two variables.
Through project management, these diagrams help identify patterns and trends that mightn’t be apparent from simply looking at the raw data. By utilizing Scatter Diagrams in data analysis, you can pinpoint potential cause-and-effect relationships, guiding your efforts toward impactful process improvements.
This visual representation method enhances your ability to make informed decisions based on concrete evidence, ultimately contributing to the success of your Six Sigma initiatives.
Statistical Process Control (SPC)
Consider implementing Statistical Process Control (SPC) as a key Six Sigma tool to monitor and maintain process stability and quality. SPC is a fundamental aspect of the Six Sigma method, ensuring that processes meet quality standards consistently.
By utilizing SPC techniques, you can identify variations in the production process that may lead to defects or inefficiencies. This allows for timely adjustments to be made, preventing quality issues before they occur.
Through the use of statistical tools within SPC, such as control charts and histograms, you can analyze data trends and make informed decisions to improve overall process performance. Embracing Statistical Process Control not only aligns with Six Sigma methodology but also enhances your ability to uphold high-quality standards efficiently.
Common Challenges and Solutions in Implementing Six Sigma
Six Sigma implementation often faces resistance from employees unfamiliar with the Six Sigma process, requiring effective Six Sigma training to educate and engage them.
Another common challenge is the lack of top management support, hindering the successful integration of the Six Sigma methodology into the organization. To address this, it’s crucial to align Six Sigma goals with the company’s strategic objectives and secure leadership buy-in.
Sustaining Six Sigma initiatives in the long term proves difficult without a robust measurement system in place to track progress and outcomes. By establishing clear metrics and regularly monitoring performance, organizations can ensure the continued success of their Six Sigma efforts.
Benefits of Implementing Six Sigma
By implementing Six Sigma, you can significantly improve efficiency and quality within the organization.
The benefits of implementing the Six Sigma methodology lie in its focus on reducing defects, enhancing customer satisfaction, and increasing overall productivity.
By adhering to Six Sigma principles, you can streamline processes, minimize errors, and achieve consistent results.
This structured approach fosters a culture of continuous improvement, where data-driven decisions lead to sustainable advancements.
Through the systematic application of Six Sigma tools and methodologies, you can pinpoint areas for enhancement, optimize operations, and boost profitability.
Embracing Six Sigma not only drives operational excellence but also cultivates a mindset geared towards excellence and customer-centricity, positioning your organization for long-term success.
Criticisms and Limitations of Six Sigma
After implementing the Six Sigma methodology and experiencing its benefits, you may encounter criticisms and limitations that impact the effectiveness of this quality improvement approach.
One limitation is the extensive training and resources required for successful Six Sigma implementation. This can strain smaller organizations with limited budgets. Some critics argue that the rigid structure of the Six Sigma process can stifle creativity and innovation within teams.
If the focus is solely on meeting specific sigma targets, there’s a risk of neglecting the broader organizational goals and customer needs. It’s important to address these criticisms by ensuring that Six Sigma is implemented thoughtfully, balancing the structured approach with the flexibility needed to adapt to changing circumstances and foster continuous improvement.
Future of Six Sigma
The future of Six Sigma holds exciting developments, such as its integration with Lean Manufacturing for enhanced efficiency.
Industry 4.0 is set to revolutionize how Six Sigma is applied, adapting to the changing technological landscape.
The service industry and the digital age present new opportunities for Six Sigma methodologies to thrive and evolve.
Six Sigma and Lean Manufacturing
Lean manufacturing focuses on eliminating waste and improving efficiency in processes, while Six Sigma methodologies aim at reducing defects and variations to enhance quality.
By combining these approaches, organizations can achieve significant improvements in both operational efficiency and product quality. The integration of Six Sigma and Lean Manufacturing is becoming increasingly popular as it allows companies to streamline processes, minimize costs, and deliver higher quality products and services to customers.
This synergy between Six Sigma and Lean Manufacturing not only optimizes operations but also fosters a culture of continuous improvement and innovation within the organization, ensuring sustained success in the ever-evolving business landscape.
Six Sigma and Industry 0
By leveraging the integration of Six Sigma and Lean Manufacturing principles, you can foresee the potential impact of Industry 0 on the future of Six Sigma methodology. As businesses continue to evolve and embrace digital transformation, the traditional Six Sigma methodology is also adapting to meet the demands of Industry 0.
This new era of connectivity and automation presents opportunities to enhance business processes through the application of lean Six Sigma principles. By leveraging data analytics, artificial intelligence, and IoT technologies, organizations can optimize their processes, drive efficiency, and deliver higher-quality products and services.
The synergy between Six Sigma and Industry 0 offers a pathway for businesses to stay competitive in a rapidly changing landscape, making continuous improvement an essential aspect of modern business methodologies.
Six Sigma in the Service Industry
When implementing Six Sigma in the service industry, you can enhance efficiency and quality through structured process improvement methodologies. By conducting a thorough analysis of business processes, you can identify areas for optimization, leading to increased customer satisfaction.
In the service industry, Six Sigma principles offer a systematic approach to business process management, ensuring that services meet or exceed customer expectations. By focusing on customer needs and streamlining operations, Six Sigma enables organizations to deliver consistent, high-quality services.
Embracing Six Sigma in the service industry not only enhances operational efficiency but also fosters a customer-centric culture that drives continuous improvement. As the service industry evolves, integrating Six Sigma methodologies becomes essential for staying competitive and meeting the ever-changing demands of customers.
Six Sigma in the Digital Age
Implementing Six Sigma in the digital age involves leveraging advanced technology and data analytics to drive continuous improvement and optimize processes for enhanced operational performance.
In the realm of Six Sigma methodology, leadership plays a crucial role in championing digital transformation and ensuring alignment with organizational goals.
Projects are now executed with a focus on utilizing digital tools for real-time monitoring and analysis, enabling quicker decision-making and problem-solving.
Training in the digital age emphasizes not only the core principles of Six Sigma but also the integration of technology and data-driven approaches.
This evolution in Six Sigma reflects a shift towards a more agile and tech-savvy approach, positioning organizations to thrive in today’s rapidly changing business landscape.
Frequently Asked Questions
Can Six Sigma Be Applied to Any Industry, or Is It More Suitable for Specific Sectors?
Six Sigma can be applied to any industry. Sigma focuses on quality improvement and reducing defects, making it valuable across sectors. Assess your industry’s needs to determine if Six Sigma aligns with your goals.
How Does the Implementation of Six Sigma Impact Company Culture and Employee Morale?
When implementing Six Sigma, you’ll notice a positive impact on company culture and employee morale. Processes become more efficient, errors decrease, and employees feel empowered by their contributions to continuous improvement, fostering a collaborative and motivated environment.
Are There Any Common Challenges or Pitfalls That Organizations Face When Adopting Six Sigma?
When adopting Six Sigma, common challenges include resistance to change, lack of leadership support, and insufficient training. Ensure clear communication, involve employees in the process, and address issues promptly to navigate these pitfalls effectively.
How Does The Six Sigma Methodology Adapt to Changes in Technology and Market Trends?
To adapt to changes in technology and market trends, the Six Sigma methodology incorporates continuous improvement practices, data analysis for informed decision-making, and regular reviews of processes. This allows you to stay agile and responsive.
What Are Some Key Differences Between Six Sigma and Other Quality Improvement Methodologies Like Lean or Total Quality Management?
To distinguish Six Sigma from Lean or Total Quality Management, focus on its data-driven approach to minimize defects and variation. Lean emphasizes waste reduction, while TQM prioritizes customer satisfaction through continuous improvement. Each has unique strengths.
Related Term | Definition |
---|---|
Certification Program | A structured program that validates the expertise of individuals in specific fields or with certain skills. |
Financial Analysis | The examination of financial data to assist in decision-making, often involving the analysis of financial statements to determine a company’s health. |
Existing Processes | The current set of procedures or methods being used within an organization or for a specific function. |
Manufacturing Processes | The steps, operations, and methods used to transform raw materials into finished products. |
Statistical Processes | Techniques and procedures used to analyze data sets to improve understanding and decision-making. |
Analyze Improve and Control | A phase within process improvement methodologies focusing on analyzing processes, implementing improvements, and establishing controls to sustain gains. |
Collecting Data | The process of gathering information or measurements for the purpose of analysis and decision-making. |
Increase Efficiency | The objective of optimizing resources to enhance productivity and reduce waste in processes. |
Increase Customer Satisfaction | Strategies and actions aimed at enhancing the customer experience, leading to higher satisfaction levels. |
Lean Management | A management philosophy focused on minimizing waste while maximizing value in the production process, often through continuous improvement. |