In today’s fast-paced and increasingly competitive business environment, the quest for perfection in product development and service quality is relentless. Companies across the globe are turning to robust methodologies to enhance their operations, reduce failures, and ensure efficient production strategies. Among these, the DMADV model, a cornerstone of the Six Sigma framework, emerges as a beacon of hope for organizations striving for excellence.
This article delves into the DMADV methodology, a structured approach that integrates the principles of lean manufacturing and Six Sigma to foster continuous improvement in the design and development of products and services. By leveraging conceptual designs, detailed models, and optimal combinations of processes, businesses can achieve unprecedented levels of quality management. From green belts to Six Sigma professionals, the insights shared here will illuminate the path to success through improved design output and the elimination of problematic processes.
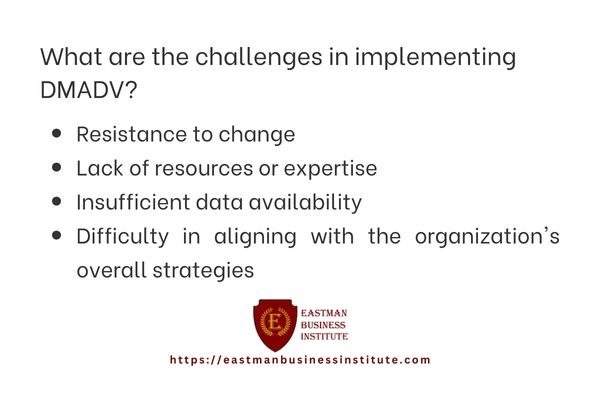
Whether you are looking to refine an existing product or develop a new one, the DMADV model offers a comprehensive guide to achieving your goals with precision and efficiency. Join us as we explore the depths of DMADV, from its theoretical foundations to its practical applications in Lean Six Sigma and beyond, and discover how it can transform your approach to product development and service delivery.
More Things To Know About DMADV Model

Understanding DMADV Model
The DMADV Model, also known as Define, Measure, Analyze, Design, and Verify, is a structured approach used to design and develop new products, services, or processes. It’s often employed in Six Sigma, a methodology aimed at improving quality and reducing defects.
The DMADV Model consists of five phases, with each phase playing a crucial role in the overall process.
The first phase, the Define phase, involves identifying the project goals, customer needs, and project scope.
The second phase, the Measure phase, focuses on collecting data and establishing performance metrics.
The third phase, the Analyze phase, involves analyzing the data to identify potential improvement opportunities.
The fourth phase, the Design phase, focuses on developing and testing potential solutions.
The fifth phase, the Verify phase, involves implementing and validating the proposed solution.
History and Development of DMADV Model
The DMADV Model was developed by the management consulting firm, Six Sigma. It’s a structured approach that aims to improve the quality and efficiency of a project by minimizing defects and variations.
The DMADV Model originated from the DMAIC Model, which focused on improving existing processes. The DMADV Model specifically targets the development of new products, services, or processes.
Over time, the DMADV Model has gained popularity in various industries, including manufacturing, healthcare, and technology, due to its systematic and data-driven approach to design and development.
Importance of DMADV Model in Six Sigma
The DMADV Model is an essential tool in Six Sigma, providing a systematic and effective approach to designing and developing new products, services, or processes. Its importance lies in the fact that it helps organizations achieve their goals of improving quality and reducing defects.
By following the DMADV Model, companies can ensure that their new initiatives meet customer requirements and are designed with efficiency and effectiveness in mind. This model enables organizations to identify and eliminate potential problems before they occur, saving time and resources. It also helps streamline processes, reduce waste, and enhance customer satisfaction.
Components of DMADV Model
In the Define phase, you’ll establish the purpose and goals of your project, as well as identify key activities to be undertaken. The expected outcomes of this phase are a clear understanding of the problem and the project scope.
In the Measure phase, you’ll gather data and metrics to assess the current state of the process or product you’re working on.
Define Phase
To begin the Define Phase of the DMADV model, you should clearly define the goals and objectives of your project. This phase is the first step in the six sigma methodology and focuses on understanding the customers’ requirements.
It’s crucial to identify what the customers want and need from the project to ensure that the final product or service meets their expectations. During the Define Phase, you’ll gather data, conduct market research, and analyze customer feedback to gain a deep understanding of their preferences and expectations.
This information will serve as a foundation for the rest of the DMADV model, guiding the decision-making process and ensuring that the project delivers value to the customers.
Purpose and Goals
You should start by clearly defining the purpose and goals of the DMADV model in order to guide your project effectively.
The DMADV model, which stands for Define, Measure, Analyze, Design, and Verify, is a systematic approach used to develop new products or processes.
The purpose of the DMADV model is to ensure that the final outcome meets the needs and expectations of the customers. It aims to reduce defects, improve quality, and increase customer satisfaction.
The goals of the DMADV model include identifying and understanding customer requirements, analyzing and improving existing processes, designing new products or processes that meet those requirements, and verifying that the final solution meets the desired outcomes.
Key Activities
After clearly defining the purpose and goals of the DMADV model, you can now move on to discussing the key activities or components of the model. These key activities play a crucial role in the successful implementation of the DMADV model.
The first component is the Define phase, where you identify the project goals, customer needs, and project scope.
In the Measure phase, where you gather data on the current process performance.
The Analyze phase follows, where you analyze the data to identify the root causes of the problems.
In the Design phase, you develop and design potential solutions to address the identified issues.
In the Verify phase, you test and validate the proposed solution before implementing it.
These key activities form the foundation of the DMADV model, ensuring a systematic and effective approach to process improvement.
Expected Outcomes
During the implementation of the DMADV model, you can expect improved process performance and successful resolution of identified issues. These outcomes are crucial for ensuring customer satisfaction, as they directly impact customer expectations and requirements.
By following the DMADV model, you can effectively identify and address any issues that may hinder your ability to meet customer needs. Through careful analysis and redesign, you can improve the overall performance of your processes, leading to higher levels of customer satisfaction.
The successful resolution of identified issues ensures that you’re able to meet and exceed customer expectations, ultimately leading to a stronger relationship with your customers.
Measure Phase
The Measure phase of the DMADV model involves quantifying and assessing key process metrics. In this phase, you’ll gather data to evaluate the current state of the process and identify any gaps or opportunities for improvement.
The main goal is to measure the performance of the process in order to establish a baseline and set targets for improvement. This is done by collecting relevant data and analyzing it using statistical tools.
The Measure phase is crucial because it provides a clear understanding of the current process performance and helps in determining the appropriate metrics to focus on during the subsequent phases of the DMADV model. By using Six Sigma principles, you can ensure that the data collected is accurate and reliable, enabling you to make informed decisions and drive meaningful improvements.
Purpose and Goals
To continue assessing and improving the current process, your next step in the DMADV model is to define the purpose and goals of the project.
This crucial phase sets the foundation for the entire project and ensures that everyone involved understands the desired outcome. The purpose clarifies why the project is being undertaken, while the goals outline specific objectives that need to be achieved.
By clearly defining the purpose and goals, you provide a clear direction for the project team and stakeholders. The purpose and goals also serve as benchmarks to measure the success of the project. They provide a framework for decision-making and help prioritize tasks and resources.
Keep in mind that the purpose and goals should be specific, measurable, attainable, relevant, and time-bound (SMART) to ensure effective project management.
Key Activities
Start by identifying the key activities that are involved in the DMADV model. These activities are essential components of the DMADV model and play a crucial role in its successful implementation.
The key activities of the DMADV model include defining, measuring, analyzing, designing, and verifying. Each of these activities is designed to guide the improvement process and ensure that it’s effective and efficient.
In the context of the DMADV model, defining involves understanding the project goals and objectives. Measuring focuses on gathering data and evaluating the current state. Analyzing involves identifying root causes and potential improvement opportunities. Designing entails creating and developing potential solutions. Lastly, verifying involves testing and implementing the finalized solution.
These key activities are contextually relevant and are instrumental in achieving the desired outcomes of the DMADV model.
Expected Outcomes
The DMADV model, also known as Define, Measure, Analyze, Design, and Verify, is a Six Sigma methodology used to develop new products or processes.
The expected outcomes of the DMADV model include improved quality, reduced defects, increased customer satisfaction, decreased costs, and enhanced productivity.
By following the DMADV model, organizations can identify and define customer requirements, measure current performance, analyze data to identify improvement opportunities, design and implement new processes or products, and verify the effectiveness of the changes made.
Analyze Phase
The Analyze Phase is a crucial step in the DMADV model, which stands for Define, Measure, Analyze, Design, and Verify. This model is part of the Six Sigma methodology, a data-driven approach to process improvement.
In the Analyze Phase, data collected during the Measure Phase is analyzed to identify the root causes of problems and opportunities for improvement. Statistical tools, such as regression analysis and hypothesis testing, are commonly used to analyze the data.
The goal is to gain insights and make data-driven decisions that will lead to the development of effective solutions. Through the Analyze Phase, the DMADV model ensures a thorough understanding of the current state of the process and identifies areas for improvement.
Purpose and Goals
In the Purpose and Goals component of the DMADV model, you’ll delve into the specific objectives and outcomes that this model aims to achieve, building upon the insights gained from the Analyze Phase.
The purpose of the DMADV model is to provide a structured approach for designing and implementing new products, services, or processes. Its goal is to ensure that the desired outcome meets or exceeds customer expectations, while also improving efficiency and minimizing defects.
Key Activities
To begin the discussion of the key activities within the DMADV model, you’ll identify and outline the specific steps required to successfully design and implement new products, services, or processes.
The DMADV model, also known as Define, Measure, Analyze, Design, and Verify, is an important framework used in Six Sigma methodology. The key activities in this model are crucial for achieving the desired results and improving quality.
Define the project goals and objectives, as well as the customer requirements.
Measure the current process performance to identify areas for improvement.
Analyze the data to uncover the root causes of any issues.
Design a new process or solution that meets the customer’s needs.
Verify the effectiveness of the design through testing and validation.
Expected Outcomes
When implementing the DMADV model, organizations can achieve four key expected outcomes.
- Improved customer satisfaction: By using DMADV, organizations can better understand customer needs and preferences, leading to the development of products and services that align with customer expectations.
- Increased efficiency: Through the DMADV process, organizations can identify and eliminate waste, resulting in streamlined processes and improved productivity.
- Reduced defects and errors: By applying the principles of Six Sigma, DMADV helps organizations identify and eliminate potential defects, ensuring high-quality products and services.
- Increased profitability: Lastly, DMADV can lead to increased profitability. By improving customer satisfaction, efficiency, and quality, organizations can enhance their competitive advantage and boost their bottom line.
Design Phase
Start by outlining the components of the Design Phase in the DMADV model. In this phase, you’ll focus on developing and evaluating potential design alternatives. This is a critical step in the DMADV model as it involves creating and refining the design solution that will meet the identified customer requirements.
During the Design Phase, you’ll consider different design options, assess their feasibility, and evaluate their potential impact on the final product. This phase also involves conducting design reviews, simulations, and prototypes to validate the chosen design.
Purpose and Goals
The DMADV model is a structured approach used for designing and implementing new products, processes, or services. Its purpose is to ensure that the end result meets customer requirements and expectations while minimizing risks and maximizing efficiency.
The goal of the DMADV model is to provide a systematic framework that guides project teams through each phase, from defining the project goals and customer needs to designing and verifying the final solution. By following this model, organizations can reduce costs, improve quality, and increase customer satisfaction.
The DMADV model is particularly effective in situations where existing processes or products aren’t meeting desired objectives or require significant improvements.
Key Activities
The key activities of the DMADV model include defining project goals and customer needs, measuring performance metrics, analyzing data, designing the solution, and verifying its effectiveness.
The DMADV approach is a systematic design process used to create new products or improve existing ones.
In the first stage, project goals and customer needs are clearly defined to understand the desired outcome.
Then, performance metrics are established to measure the success of the project.
Next, data analysis is conducted to identify areas of improvement and potential solutions.
The design process follows, where the solution is developed and refined.
Lastly, the effectiveness of the solution is verified through testing and feedback.
Expected Outcomes
To achieve the desired outcomes, the components of the DMADV model involve clear project goals, well-defined customer needs, established performance metrics, data analysis, solution design, and effective verification.
The DMADV model, which stands for Define, Measure, Analyze, Design, and Verify, is a Six Sigma methodology used to develop new products, services, or processes.
The expected outcomes of implementing the DMADV model include improved customer satisfaction, reduced defects and errors, increased efficiency, and enhanced profitability.
By clearly defining project goals and understanding customer needs, organizations can align their efforts towards meeting and exceeding customer expectations.
Established performance metrics allow for objective evaluation and measurement of progress, while data analysis provides insights and informs decision-making.
Solution design ensures that the final product or process meets customer requirements, and effective verification ensures that the solution is implemented correctly and meets the desired outcomes.
Verify Phase
In the Verify phase of the DMADV model, you’ll evaluate the implemented solution to ensure it aligns with the desired outcomes.
This phase is crucial in the DMADV model as it allows you to validate the effectiveness and efficiency of the solution before fully implementing it.
By conducting thorough evaluations and measurements, you can verify if the solution meets the predetermined criteria and if it addresses the identified problem.
This phase also involves comparing the actual results with the expected outcomes to determine if any adjustments or improvements are needed.
The Verify phase aligns with the principles of Six Sigma, which aims to minimize defects and variations in processes.
Through this phase, you can ensure that the implemented solution not only meets the desired outcomes but also adheres to the rigorous standards of Six Sigma.
Purpose and Goals
When applying the DMADV model, you can achieve your purpose and goals by utilizing its components.
The DMADV process, also known as the Six Sigma improvement process, is designed to help organizations develop new products or services that meet customer requirements and deliver exceptional quality.
The purpose of DMADV is to ensure that the final solution isn’t only effective but also efficient. Its goal is to minimize defects and variations, reduce waste, and optimize processes.
By following the DMADV process, you can identify and understand customer needs, design and develop innovative solutions and validate their effectiveness before implementing them.
This systematic approach helps organizations achieve their purpose of delivering high-quality products and services while meeting customer expectations.
Key Activities
First, identify the key activities involved in the DMADV model to effectively implement the Six Sigma improvement process.
The DMADV model, which stands for Define, Measure, Analyze, Design, and Verify, is a systematic approach used to develop new products, services, or processes.
In the Define phase, the project goals, scope, and customer requirements are established.
The Measure phase involves collecting data on the current process performance and identifying areas for improvement.
In the Analyze phase, the data is analyzed to identify root causes of problems and potential solutions.
The Design phase focuses on developing and implementing the new process or product.
Finally, the Verify phase ensures that the new process meets customer requirements and is capable of delivering the desired results.
Expected Outcomes
Achieve desired outcomes by implementing the DMADV model, which includes five key components:
- Define: This involves defining the project goals and customer requirements. It is essential to clearly understand what needs to be achieved and what the customer expects.
- Measure: The second step is to measure the current performance. This involves collecting data and metrics to assess the current state of the process or product.
- Analyze: Once the data is collected, it is analyzed to identify improvement opportunities. This step helps in understanding the root causes of any problems or defects.
- Design: After analyzing the data, the next step is to design and develop the new solution. This involves creating a plan or blueprint for the improved process or product.
- Verify: The final step is to verify the effectiveness of the new solution. This involves testing and evaluating the results to ensure that the desired outcomes have been achieved.
The expected outcomes of implementing the DMADV model are improved quality, reduced defects, increased customer satisfaction, optimized processes, and enhanced profitability.
DMADV vs DMAIC
Both methodologies are used in process improvement and have a structured approach.
While DMAIC is more suitable for improving existing processes, DMADV is used to develop new processes or products.
It’s important to consider the specific needs and goals of your project to determine whether to use DMADV or DMAIC.
Similarities between DMADV and DMAIC
The DMADV model and DMAIC are both methodologies used in Six Sigma, a process improvement approach. While DMADV focuses on designing new processes, products, or services, DMAIC is used to improve existing processes.
Both models follow a structured approach, consisting of five phases: Define, Measure, Analyze, Improve, and Control. The main goal of both DMADV and DMAIC is to reduce defects, improve customer satisfaction, and increase efficiency.
Both models utilize data-driven decision making and statistical tools to identify and solve problems. By implementing either DMADV or DMAIC, organizations can achieve significant improvements in quality and performance.
Understanding the similarities between DMADV and DMAIC is crucial for selecting the most appropriate approach for process improvement.
Differences between DMADV and DMAIC
Comparing DMADV and DMAIC highlights the distinctions between the two methodologies used in Six Sigma. While both approaches aim to improve processes and reduce defects, they differ in their application and focus.
The DMADV model, which stands for Define, Measure, Analyze, Design, and Verify, is primarily used for creating new products or processes. It’s a structured approach that emphasizes the development and implementation of new solutions.
DMAIC, which stands for Define, Measure, Analyze, Improve, and Control, is used to improve existing processes. It focuses on identifying and eliminating sources of variation and waste.
Understanding these differences is crucial in selecting the right methodology for the contextually relevant situation and ensuring the success of Six Sigma initiatives.
When to Use DMADV vs DMAIC
To determine whether to use DMADV or DMAIC, consider the specific circumstances and goals of your project. Both methodologies have their own strengths and are suited for different situations. DMADV is typically used when starting a new project or when the existing process needs a complete overhaul. It is a more structured approach that focuses on designing a new process or product from scratch.
DMAIC is ideal for improving existing processes that are not meeting desired performance levels. It is a problem-solving methodology that aims to identify and eliminate root causes of problems.
To help you decide which approach to use, here is a comparison table of DMADV and DMAIC:
DMADV Model | DMAIC Model |
---|---|
Define project goals and customer requirements | Define project goals and problem statement |
Measure process performance and collect data | Measure current process performance |
Analyze data to identify potential causes of problems | Analyze data to identify root causes of problems |
Design an improved process or product | Improve the existing process |
Verify and validate the design | Control and sustain the improved process |
Tips for Effective DMADV Implementation
There are several key points to consider when effectively implementing the DMADV model.
It’s crucial to thoroughly prepare for the implementation process, ensuring that all necessary resources and stakeholders are in place.
It’s important to avoid common mistakes that can hinder the success of the implementation, such as rushing through the phases or neglecting to gather sufficient data.
Following best practices for each phase of the DMADV model will help ensure a smooth and successful implementation.
Preparing for DMADV Implementation
Before implementing DMADV, it’s essential to regularly assess your organization’s readiness and capacity for change. To prepare for DMADV implementation, start by familiarizing yourself with the DMADV model and its principles.
Understand the six sigma methodology, which DMADV is a part of, and its focus on process improvement and reducing defects.
Evaluate your organization’s current processes and identify areas that require improvement. Engage key stakeholders and communicate the benefits of DMADV implementation.
Develop a clear plan and set realistic goals for the implementation process. Allocate necessary resources, such as time, budget, and personnel, to support the implementation.
Provide training and support to employees to ensure they’re equipped with the necessary knowledge and skills.
Regularly monitor progress and make adjustments as needed to ensure successful DMADV implementation.
Common Mistakes to Avoid
To ensure effective DMADV implementation, it’s important to avoid common mistakes that can hinder the process. When using the DMADV model, there are several key mistakes that you should be aware of and steer clear of.
One common mistake is rushing through the Define phase without fully understanding the problem or customer requirements. Skipping this step can lead to a flawed solution.
Another mistake is neglecting to involve key stakeholders throughout the entire process. Their input is crucial for successful implementation.
Failing to allocate adequate resources and time can hinder the effectiveness of the DMADV model.
Overlooking the importance of data analysis and relying solely on intuition can lead to poor decision-making.
Best Practices for Each Phase of DMADV
To effectively implement the DMADV model, it’s important to follow best practices for each phase, ensuring a successful outcome.
In the Define phase, clearly identify the project goals, customer requirements, and project scope. This will provide a clear direction for the entire DMADV process.
During the Measure phase, collect and analyze relevant data to gain insights into the current process and identify areas of improvement.
In the Analyze phase, use tools like root cause analysis and process mapping to understand the underlying causes of the identified issues.
The Design phase involves brainstorming and developing potential solutions that meet customer requirements.
In the Verify phase, test and implement the chosen solution, monitoring its effectiveness and making adjustments if necessary.
Future of DMADV Model
You’ll discover the current trends in DMADV implementation, including how organizations are embracing this approach to improve their processes.
We’ll also look at the predicted changes and developments in the DMADV model, considering how it might evolve to meet the changing needs of industries.
Current Trends in DMADV Implementation
Implementing the DMADV model is essential for staying up-to-date with current trends and ensuring the future success of your organization.
The DMADV model, which stands for Define, Measure, Analyze, Design, and Verify, is a systematic approach used to develop new products or processes with the aim of achieving high performance and customer satisfaction.
In today’s rapidly changing business landscape, organizations are constantly seeking ways to improve their operations and deliver superior value to their customers.
By implementing the DMADV model, you can effectively address the challenges and complexities of the ever-evolving market.
Some current trends in DMADV implementation include the increased use of data analytics to drive decision-making, the integration of design thinking principles, and the adoption of agile methodologies.
Predicted Changes and Developments
By embracing the predicted changes and developments, you can ensure the future success of your organization with the DMADV model.
As technology continues to advance, the DMADV model is expected to undergo various enhancements and improvements. One of the predicted changes is the integration of artificial intelligence and machine learning into the DMADV process. This will enable organizations to analyze large volumes of data more efficiently and make data-driven decisions.
There will be a greater emphasis on customer-centricity and user experience in the DMADV model. Organizations will strive to deeply understand their customers’ needs and preferences to develop products and services that truly fulfill their requirements.
These developments will ultimately lead to increased efficiency, enhanced customer satisfaction, and improved overall organizational performance with the DMADV model.
Impact of Technology on DMADV Model
The future of the DMADV model will be shaped by the impact of technology.
As technology continues to advance at a rapid pace, it’s inevitable that it will have a significant influence on the way the DMADV model is implemented and executed.
With the rise of artificial intelligence, machine learning, and automation, the DMADV process can be enhanced and streamlined.
Technology can help in collecting and analyzing large amounts of data, making the decision-making process more efficient and accurate.
Advancements in communication technology allow for real-time collaboration and feedback, enabling teams to work together seamlessly, regardless of geographical locations.
Technological tools and software can be utilized to facilitate the implementation and monitoring of the DMADV model, ensuring that projects are completed successfully and on time.
Frequently Asked Questions (FAQs)
What Are the Key Differences Between the DMADV Model and the DMAIC Model?
The key differences between the DMADV model and the DMAIC model lie in their approaches. DMADV focuses on designing new processes, while DMAIC focuses on improving existing processes.
Can the DMADV Model Be Applied to Any Industry or Is It Specific to Certain Sectors?
Yes, the DMADV model can be applied to any industry. It is not specific to certain sectors. This model focuses on designing new processes or products and can help improve efficiency and effectiveness in various industries.
Are There Any Potential Drawbacks or Limitations to Using the DMADV Model?
There may be potential drawbacks or limitations to using the DMADV model. It’s important to consider factors such as resource availability, time constraints, and the willingness of stakeholders to adapt to new processes.
What Are Some Real-Life Examples of Successful Implementation of the DMADV Model?
In real-life, you can find successful examples of implementing the DMADV model. It has been used to streamline processes, improve product quality, and increase customer satisfaction in various industries such as manufacturing and healthcare.
How Does the DMADV Model Contribute to Overall Business Improvement and Growth?
The DMADV model contributes to overall business improvement and growth by providing a structured approach to identify and implement new processes or products, resulting in enhanced efficiency, customer satisfaction, and increased profitability.
Related Term | Definition |
---|---|
Business Model | A framework for creating economic, social, and/or other forms of value. The process includes the identification of revenue streams, customer base, products, and financing details. |
Design for Six Sigma (DFSS) | An approach to design or redesign products or services from the ground up at Six Sigma quality levels. It is used to meet customer needs and process capability simultaneously. |
DMADV | A data-driven quality strategy for improving processes, centered on five phases: Define, Measure, Analyze, Design, and Verify. It is an integral part of the Design for Six Sigma methodology. |
Failure | The inability of a product, service, or process to meet a specified criterion, which can include defects, errors, or the lack of reliability or functionality. |
Green Belt | A professional who is trained in Six Sigma methodologies and tools, and leads small-scale improvement projects within their organization. |
Theory of Constraints | A management philosophy that focuses on identifying and removing the constraint (bottleneck) that significantly hinders a system’s performance, to improve the overall process. |